017
Reviving Traditional Crafts: Tie-ups and Development of the Production Centers Collaboration Project
The two-year Production Centers Collaboration Project was launched at the 2014 31st Traditional Craft Products Month National Assembly (Saga Assembly), and is on track to complete in 2016. The project explores the exciting possibilities of collaboration between Saga, home of Imari and Arita porcelain, and regional artisans of different traditional crafts; the innovative results of this fusion will be made available all over Japan and the world.
Imari and Arita porcelain in collaboration with eight craft traditions
"Even an article made in the past, if it has genuine value, will always contain something novel."
The traditional crafts of Japan include such diverse materials as ceramics, dyed and woven textiles, lacquerware, paper, wood and bamboo. Muneyoshi Yanagi, renowned for starting the folk-arts (craft) movement in the 1920s, was one of the first to discover the "aesthetic appeal" of the many different regional folk crafts of Japan; he was a strong advocate of such crafts and promoted new possibilities and ways of appreciating them in modern life. The hidden potential and depth and warmth of such crafts are continually fascinating whatever the era. The Production Centers Collaboration Project between Imari and Arita porcelain and other regions of traditional craftworks started at the November 2014 31st Traditional Craft Products Month National Assembly (Saga Assembly) held in Saga Prefecture; this event heralded the beginning of our current-day "craft" movement project from Saga, in the hope of a continuous and nationwide expansion of the re-evaluation of traditional crafts and regeneration of producing areas.
The 2015 32nd Traditional Craft Products Month National Assembly (Toyama Assembly) was held in Toyama Prefecture, and the project presented some of collaborative works between Imari and Arita porcelain and the following eight crafts and regions: Oshima Pongee from Kagoshima; Edo Cut Glass from Tokyo; Echizen Washi paper from Fukui; Ryukyu Ikat from Okinawa; Wajima-nuri Lacquerware from Ishikawa; Takayama Tea Whisks of Nara; Inami Woodcarving from Toyama; and Kishu Lacquerware of Wakayama. The wide-ranging works were produced in several ways such as by taking a signature motif of a regional craft, and incorporating it onto a ceramic ware design, or evolving from the concept of a bowl or vase turning into an interior objet; these works are now drawing much attention from traditional artisans and production areas of traditional handicrafts.
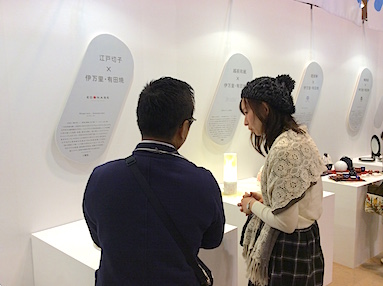
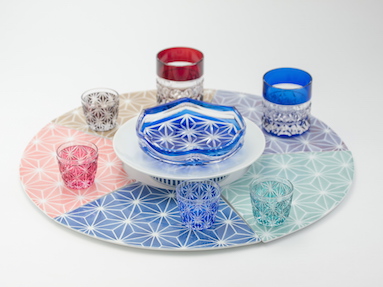
Combining different materials: A time of trial and error
It took nearly two years of painstaking repeated trial and error to produce the prototypes. The project firstly began with artisans visiting each other's production area to understand their history, skills, and the current situation of their craft. A common theme in all regions was the shortage of successors, naturally giving rise to apprehension about the future, but at the same time, project members came in touch with the living "skill" history and the strong "determination" of artisans to keep their beloved crafts alive today. It was an opportunity for creators to reflect on their own environment, and discover how fellow artisans are meeting the challenges of modern society. Each artisan also faced the challenge of working in a completely new medium and dealing with such different materials as fabric, glass, metal, or lacquer. Slowly ideas for new products started to take shape: "Echizen Washi diffuses light beautifully," "Let's apply a simple ikat design to the blue-and-white porcelain," or "The seven jewels of Edo Cut Glass can also be seen on Nabeshima porcelain, but the hemp leaf pattern, that is something different"; the artisans really enjoyed discovering the techniques of different disciplines. The possibility of presenting new innovative products suitable for the "tea ceremony (movement)" was also discussed. Later in the brush-up stage of the development process, graphic and sales-promotional designers joined with industrial designers, and played a key role in solving such problems as moving from small batch production to bulk production in the studio. A new concept was also incorporated into some products, namely, meeting the challenge of selling overseas where lacquerware is not typically used as tableware.
Completed products to be announced in September: Brush-up is now in the final phase
Hiroshige Akase, the representative of the Made in Japan Project company, and the coordinator of the Production Centers Collaboration Project commented: "The regions who collaborated with Arita, in the first place, had a strong commitment, 'If Arita's in, we're in.' In the first year, artisans exchanged visits to their production centers and experimented with prototypes, and as a result of their efforts, in the second year, designers joined in to help solve any remaining problems. The production areas are grateful for these collaborative opportunities and looking forward to making the products available. This year is the final chapter of the project, and I will continue to focus on the success of Arita." Naturally some of the eight regions are further down the road to brushing up their work than others, but we will be presenting the completed products to the public in September. The day when we take these traditional crafts from the Imari and Arita region and dispatch them out across Japan and the world is fast approaching.
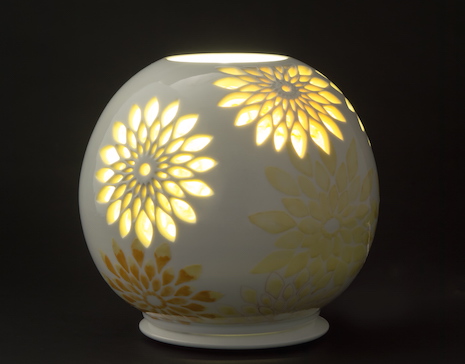
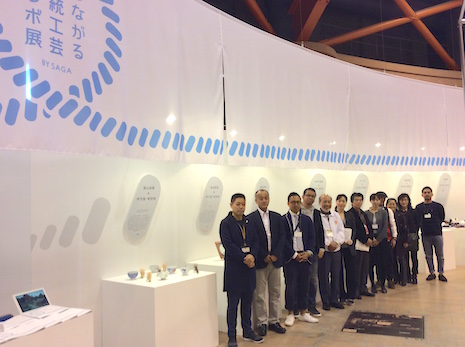